Pump convert the mechanical energy into hydraulic energy in a hydraulic system. This mechanical energy is delivered to the pump through prime mover and which result in creating partial vacuum. With build up partial vacuum permit atmospheric pressure to force and fill-up the fluid in to inlet line and pump. Then continuous mechanical action pushes the filled fluid into hydraulic system to transferring fluids location to location
Pump Capacity
Pump capacity refers to the amount of fluid that a pump can move per unit of time. It is typically measured in gallons per minute (GPM) or liters per minute (LPM). The pump capacity of a particular pump depends on several factors, including the size of the pump, the type of fluid being pumped, the pressure and flow rate required, and the overall efficiency of the pump.
Pump capacity is an important consideration when selecting a pump for a particular application. If the pump capacity is too low, it may not be able to meet the flow rate and pressure requirements of the system. On the other hand, if the pump capacity is too high, it may be unnecessarily large and expensive for the application, and may also result in higher energy consumption.
Classification of Pumps
Mainly there are two type of pumps, which are,
- Dynamic ( Nonpositive Displacement) Pump
- Positive Displacement Pump
Although there are some other classification, that categories the hydraulic pump are,
- Classification based on Fixed & Variable delivery rate
- Classification based on Rotary & Reciprocating type
- Classification based on Reversible & Non-reversible type
Dynamic (Non-positive Displacement) Pump
Dynamic pumps are a type of non-positive displacement pump, which means that they do not rely on a fixed volume to move fluid from one place to another. Instead, they use kinetic energy to generate flow.
There are several types of dynamic pumps, including centrifugal pumps, axial flow pumps, and mixed flow pumps. Centrifugal pumps are the most common type of dynamic pump and are used in a wide variety of applications, including irrigation, water treatment, and industrial processes. They work by using an impeller to accelerate the fluid, which is then converted into flow by the pump casing.
Axial flow pumps, also known as propeller pumps, use a rotating impeller with blades to move the fluid. They are commonly used in low-flow, high-head applications, such as flood control and irrigation.
Mixed flow pumps are a hybrid of centrifugal and axial flow pumps and are suitable for medium-flow, medium-head applications.
Dynamic pumps have several advantages over positive displacement pumps, including the ability to handle fluids with high viscosity, low pressure, and high flow rates. They are also generally more efficient and require less maintenance than positive displacement pumps. However, they are not as precise in terms of flow rate and may not be suitable for applications that require precise flow control.
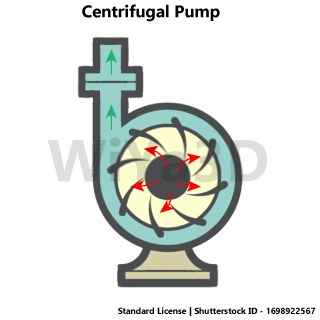
When the resistance start to increase in external system, the fluids tend to slips back into the clearance spaces. Which causing reduce in discharge flow rate. This slippage is due to the fact that fluid follows the least resistance path. When the external system resistance in too high to handle for the pump capacity, then pump will not produce flow.
Since there is a great deal of clearance between the rotating and stationary elements. The dynamic pumps are not self priming unlike positive displacement pumps.
Positive Displacement Pumps
A positive displacement pump is a type of pump that moves a fixed volume of fluid with each revolution or stroke of the pump. This is in contrast to dynamic pumps, which do not have a fixed volume and rely on kinetic energy to generate flow.
Positive displacement pumps are commonly used in applications where precise flow control is required, such as metering and dosing. They are also often used in high-pressure systems and in situations where the viscosity of the fluid is high.
There are several types of positive displacement pumps, including reciprocating/piston pumps, rotary/gear pumps, and diaphragm pumps.
There are three main type of positive displacement pumps
01. Gear Type Pump
- External gear pump
- Internal gear pump
- Lobe pump
- Screw Pump
02. Vane Type Pump
- Unbalanced Vane (fixed or variable ) pump
- Balanced Vane ( fixed displacement) pump
03. Piston Pump
- Axial pump
- Radial pump
Positive displacement pumps have a number of advantages, including their ability to handle high pressures and viscous fluids, as well as their precise flow control. However, they can be more expensive and require more maintenance than dynamic pumps.
Advantage of Positive Displacement Pumps
- High pressure capacity & handling capability
- Precise flow control
- Handle high viscous fluids
- Compact size
- High efficiency
Although they can be more expensive and require more maintenance than dynamic pumps.
Pump Classification Based on Fixed & Variable Delivery Rate
Fixed displacement pump deliver the almost constant volumetric output of fluid per revolution within same speed. While variable displacement pump the output varied by making some adjustment in internal mechanism. Thereby axial piston pump is categories as variable displacement pump.
Pump Classification Based on Rotary & Reciprocating Type
In rotary pumps, main pump moving component is rotary type and which rotating mechanism carries the liquid from suction side to discharge. Centrifugal, Gear, Lobe, Screw & Vane pumps are rotary type. On the other-hand pump mechanism with Piston categories as reciprocating type.
Pump Classification Based on Reversible & Non-Reversible Type
Pump that can be used in both direction ( suction – discharge) are called as reversible pumps.
Centrifugal Pump
A centrifugal pump is a type of dynamic pump that uses a rotating impeller to accelerate and convert the kinetic energy of a fluid into flow. It is one of the most widely used types of pumps in industry and is commonly used in applications such as water treatment, irrigation, and industrial processes.
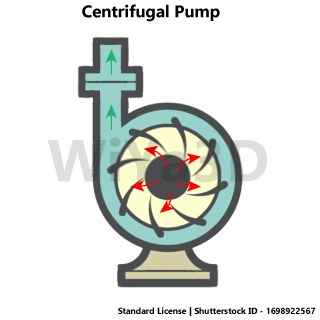
The operation of a centrifugal pump can be described as follows:
- The fluid enters the pump through an inlet, called the suction port, and is directed towards the center of the impeller.
- The impeller, which is mounted on a shaft and is typically driven by an electric motor, rotates at high speed, causing the fluid to be accelerated and forced outward towards the pump casing.
- The fluid is then converted into flow by the pump casing, which is shaped to direct the fluid in the desired direction.
- The fluid exits the pump through an outlet, called the discharge port, and is then transported to its destination.
Centrifugal pumps are known for their high flow rates and are typically used in low- to medium-pressure applications. They are also relatively easy to maintain and operate, and are available in a wide range of sizes and materials to suit different applications. However, they are not suitable for pumping fluids with high viscosities or those that contain solids, as the impeller may be damaged.
Application
- Household water pumping & Industrial general water pumping
- Agricultural water pumping
External Gear Pump
An external gear pump is a type of positive displacement pump that uses two meshed gears to move fluid from the suction side to the discharge side of the pump. It is a rotary pump, meaning that it relies on a rotating element to move the fluid.
In an external gear pump, one gear is the drive gear, which is driven by an electric motor or other power source, and the other is the driven gear. The gears are meshed together and rotate in opposite directions, with the teeth of one gear fitting into the spaces between the teeth of the other gear. As the gears rotate, they trap a small volume of fluid between them and the pump casing, and this volume is moved from the suction side to the discharge side as the gears rotate.
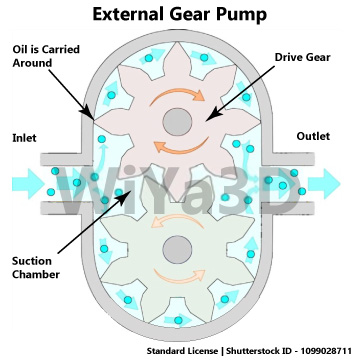
The external gear pump with spur gears are noisy at relative high speed running. In order to reduce noise it can see helical gears are used in some of pumps. And this pump is reversible pump.
Application
- Water pumping
- Industrial power hydraulic/lifting system
- Fuel & Lubricant oil transferring
- Polymer & Resin transferring
- Chemical & Additive mixing & transferring
- Alcohol & Solvent transferring
Volumetric Displacement & Flow Rate of External Gear Pump
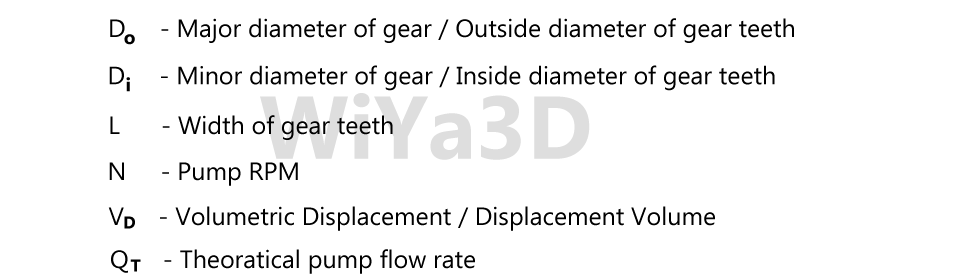

Internal Gear Pump
An internal gear pump is a type of rotary positive displacement pump that uses a pair of gears to deliver fluid from the inlet port to the outlet port. The gears are meshed together and rotate inside a casing, with one gear being the driven gear and the other being the idler gear. As the driven gear rotates, it traps a volume of fluid between the teeth of the two gears and the casing, and then pushes that volume of fluid out through the outlet port as the gears continue to rotate.
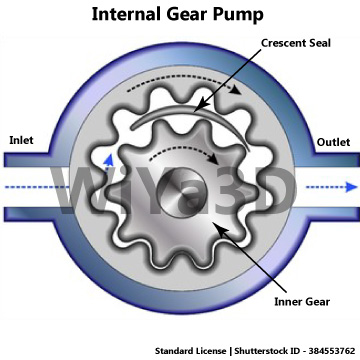
This pump has low noise compare with external pump while operation. Because suctioning pressure spread over number of teeth of gears. Internal pump also reversible pump.
Application
- Food product & Beverage
- Fuel & Lubricant oil transferring
- Polymer & Resin transferring
- Chemical & Additive mixing & transferring
- Alcohol & Solvent transferring
Lobe Pump
A lobe pump is a type of rotary positive displacement pump that uses a pair of lobes, or rotors, to move fluid from the inlet port to the outlet port. The lobes are shaped like a cam and rotate inside a casing, with one lobe being the driving lobe and the other being the driven lobe. As the lobes rotate, they create a series of pockets that trap and transport the fluid from the inlet to the outlet.
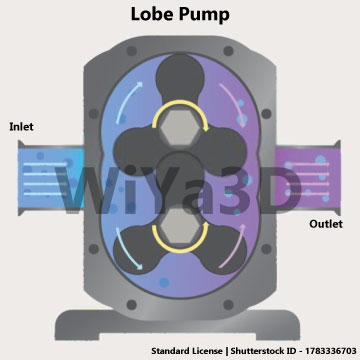
Lobe pumps are known for their ability to handle high viscosity fluids, as well as fluids with small solids or particles. They are also able to deliver a high flow rate and can operate at high pressures. Lobe pumps are often used in industries such as food processing, pharmaceuticals, and chemical processing.
One of the main advantages of lobe pumps is their ability to run at low speeds, which reduces wear and tear on the pump and increases its overall lifespan. They are also relatively simple in design and easy to maintain, which makes them a popular choice in a variety of applications.
Application
- Soap Industry
- Paint & Dye
- Food
- Polymer & Resin
- Rubber
Gerotor Pump
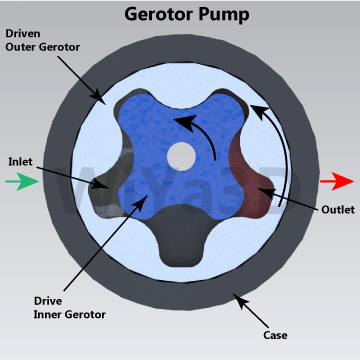
Gerotor pump operate very similar manner in internal gear pump. inner and outer gerotor mesh together and when the inner gerotor driven through prime mover, the external gerotor draws around. This meshing arrangement for gerotor makes the inlet and outlet chambers. The sealing between inlet to outlet chamber obtain with contact of inner-outer gerotors. This inner gerotor has less than one teeth of external gerotor. Therefore pump volumetric displacement is determined by space formed by extra tooth in outer rotor. This pumps are reversible.
Application
- Light fuel & Lubricant oil
- Cooking oil
Screw Pump
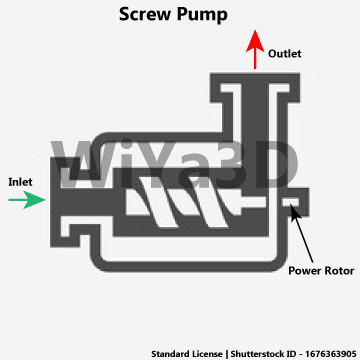
Screw pump is axial flow positive displacement pump, which consists of two to three helical screws with precision meshing. The fluid is carried in the gaps between screws. Screw pump provide the smoothest & quiet flow of fluids. However these pumps are not reversible.
Application
- Heavy oil pumping
- Heavy duty lifting application
- Lubrication oil
- Gas & Mining industry
Vane Pump
Vane pump is fixed displacement pump. The pump contain the rotor with contained radial slots attached with vane. This vane can radial move in – out. This rotor eccentrically mounted in ring housing. During rotation of rotor one half volume increase between ring housing & rotor. Which result in pressure drop in that half and suction process start and cause fluid to flow through the inlet. With continue rotation raped fluid volume is reduced and pressurized fluid pushed from discharge port.
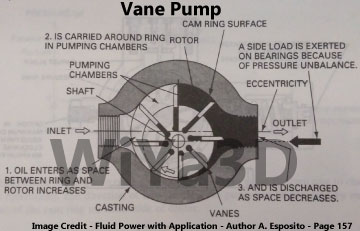
Vane pump is variable displacement pump in such a way pump can design mechanically varying the eccentricity to archive variable volumetric displacement.
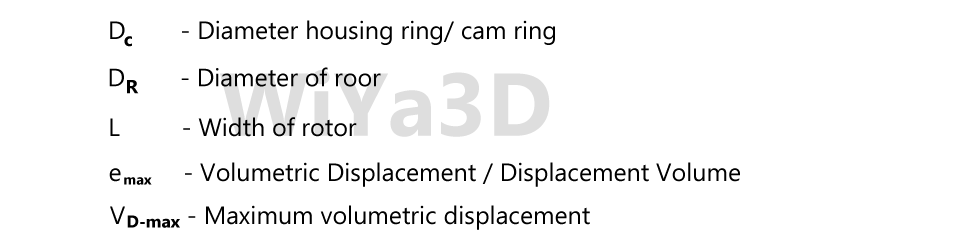

Application
- LPG gap
- Lubricant
- Petroleum & Gasoline
- Light fuel & oils
- Alcohol
- Refrigerant
Balanced Vane Pump
This pump, pump housing ring is made in such a way that oval shape. In that case vanes reciprocating motion happen in two times per revolution of rotor. That pump has two inlet and outlet ports diametrically opposite to each other. Due to this double motion and double pumping action the pressure & force balance on the rotor and called the balanced vane pump. However balanced vane pump cannot be designed to archive variable displacement.
Reciprocating Pump / Piston Pump
Reciprocating pump are more efficient at high pressure operation such as 150 bar or more. This pump operate when the piston retract the reciprocating mechanism, the fluid draws and discharge when it extend. The piston pump categories as single piston or with multiple piston. While multiple piston further divide axial piston pump and radial piston design.
Axial Piston Pump ( Straight Axis or Bent Axis)
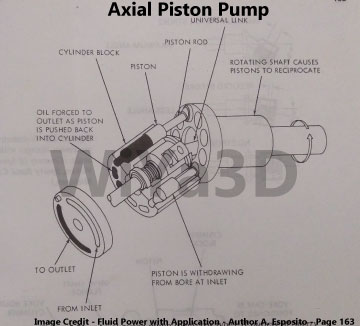
When the piston move along the drive shaft axis is called straight axis axial pump. The multiple pistons are connected with shoe plate, which is rotate with drive shaft and with shoe plate angle the piston reciprocation happen. The fixed position inlet-outlet port slots are machined in pump body against the shoe-piston plate. When the each piston pass the inlet port it draw the fluid and when pass the outlet port discharge the fluid inside piston with reciprocating action.
When the axis of drive shaft and axis of piston inclined each other those designed pump called axial piston pump. While pump operation is same as straight axis piston pump.
All these axis piston pump are variable displacement & reversible pumps. That the shoe plate angle can adjust in mechanically to archive different displacement of volume.
Application
- Hydraulic system of aircraft
- Automotive air-conditioning system
Radial Piston Pump
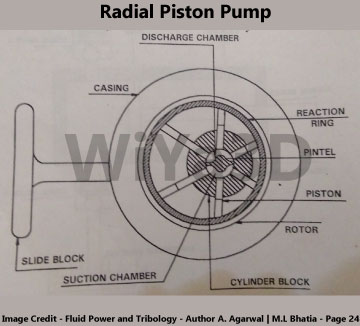
In this pump there is stationary pintle, which serve as valve that directing fluid in & out. Then there is rotating cylinder barrel with piston rotating around the pintle. Rotor containing a reaction ring which constantly rub the piston heads. During pumping action cylindrical block eccentrically rotate with prime mover and rotor rotate with friction of reaction ring. With rotation piston draw the fluid from suction port and rest of the rotation half of the piston the fluid discharge at discharge port.
Slide block control used to control the piston stroke length to archive variable displacement of volume. And use for high pressure operation such as 400 bar or above.
Application
- Mineral oil pumping
- High pressure overload protection units
Pump Performance
Mainly pump performance determined by pump type and manufacturing precision. In theory the all assembly parts/sealing parts need to have zero clearance & no friction. Although this is not possible to archive in manufacturing & assembly process. Therefore in order to archive optimum balance in pump manufacturability and performance proper sealing, oil film &/or lubricants are used in between rubbing parts.
Volumetric Efficiency
This indicate the amount of leakage in the pump.

Mechanical Efficiency
Indicate the energy losses other than the leakage issue

Generally gear pumps are simple in design, compact size and less expensive, but provide the lowest performance. Overtime gear pump efficiently reduce with wear. Therefore maintenance cost is high.
Volumetric efficiency of gear pump affected by,
- Leakage across gear faces
- Leakage around gear outer periphery
- Leakage at gear teeth contacts
Most expensive pumps are piston pumps. However high performance level can be archive at high speed operation (up to 5000 rpm). Piston pump can operate at high level of pressure. This pump has complex design and generally it’s difficult to repair.
Pump Selection Consideration
- Flow rate requirement
- Pressure rating
- Operating speed
- Performance
- Pump maintenance & maintenance cost
- Reliability
- Cost
- Noise