Manufacturing refers to the process of turning raw materials into finished products. The specific manufacturing process used can vary depending on the type of product being made and the equipment and facilities available. Some common steps in the manufacturing process include:
- Design: The first step in the manufacturing process is to create a design for the product. This may involve creating blueprints, drawings, or computer-aided design (CAD) models.
- Raw materials: The next step is to gather the raw materials needed to make the product. These materials may include metals, plastics, or other materials, depending on the product being made.
- Tooling: In some cases, specialized tools or equipment may be needed to manufacture the product. These may include molds, dies, or other specialized equipment.
- Assembly: The raw materials are then assembled into the final product. This may involve various manufacturing processes such as machining, welding, or injection molding.
- Testing: Once the product has been assembled, it is typically tested to ensure that it meets quality and performance standards.
- Packaging: Finally, the finished product is packaged and prepared for shipping to customers.
There are many different manufacturing processes that can be used, and the specific process used will depend on the product being made and the resources and equipment available.
Conventional manufacturing Processes are:
- Casting Process
- Forging Process
- Machining Process
- Rolling Process
- Extrusion
- Wire and Bar Drawing Process
- Sheet Metal Working
- Powder Metallurgical Process
- Additive Manufacturing (Rapid Prototyping, 3D Printing,..)
Casting Process
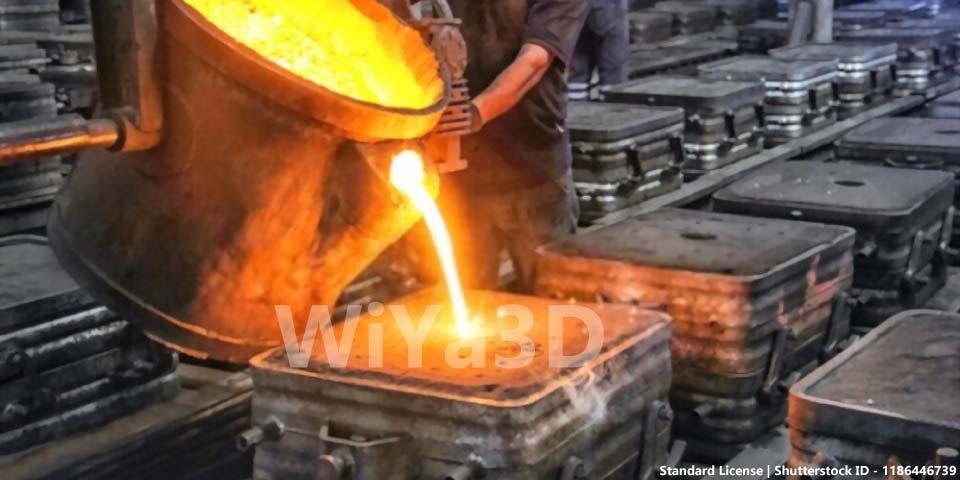
Casting is a manufacturing process in which molten metal is poured into a mold and allowed to solidify, taking on the shape of the mold. It is a versatile process that can produce a wide range of shapes and sizes, and is used to create everything from engine blocks to jewelry.
There are several different types of casting processes, each with its own set of advantages and disadvantages. The most common types of casting include:
- Sand casting: This is the most basic and oldest form of casting, in which sand is packed around a pattern to create the mold. The pattern is then removed, and the molten metal is poured into the mold. The sand is reused for multiple castings, making it a cost-effective process. However, the surface finish of the casting may not be as smooth as with other methods.
- Investment casting: This process, also known as lost-wax casting, involves creating a wax pattern of the desired object, which is then encased in a ceramic material. The wax is melted out of the mold, and the molten metal is poured in to take its place. This process produces high-quality, detailed castings with a smooth surface finish.
- Die casting: In this process, the molten metal is forced into a steel mold under high pressure. The mold is typically cooled with water to speed up the solidification process. Die casting is often used to produce large quantities of small, complex-shaped parts with a high level of accuracy and a smooth surface finish.
- Permanent mold casting: This process is similar to die casting, but the mold is made of metal and can be used for multiple castings. The molten metal is poured into the mold and allowed to solidify. Permanent mold casting is often used to produce parts with a high level of accuracy and a smooth surface finish.
Regardless of the type of casting process used, the first step is always to create the mold. This is typically done using a pattern, which is a replica of the desired object. The pattern can be made of wood, metal, or plastic, and is used to create the mold. Once the mold is created, the molten metal is poured into it and allowed to solidify.
After the casting has cooled and hardened, it is typically machined to achieve the desired dimensions and finish. The casting may also be subjected to heat treatment to improve its strength and other properties.
Overall, the casting process is a powerful tool for creating a wide range of objects and parts, from large engine blocks to small jewelry items. It is a versatile process that is widely used in a variety of industries, including automotive, aerospace, and construction.
Terminologies Used for Casting Process
There are two processes of casting processes:
- Expendable mold process
- Permanent mold process
In expending mold process, mold is usually destroyed to remove the casting (desired part). Examples of this type of process include sand casting. In permanent mold casting, mold is made up of metal and one mold is used to produce many castings.
Applications
Casting is a widely used manufacturing process that is used in a variety of applications. A few of these applications are given below:
- Body of Automobile Vehicles
- Frames of Machines
- Burning stoves
- Large statues
- Large bells used in Church
- Pipes and pipe joints
- Housings for Reciprocating Pumps
- Silver and Gold Jewelry
- Dental Crowns
Forging Process
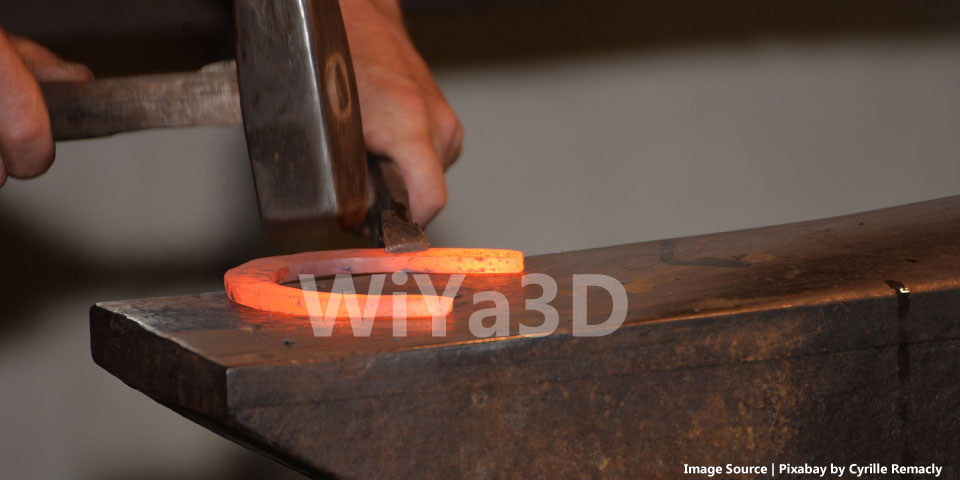
Forging is a manufacturing process in which metal is shaped by hammering, die pressing, or rolling. It is a traditional method of forming and shaping metal that has been used for centuries to produce a wide range of objects, from simple tools to complex machinery.
Forging can be performed as hot, warm, or cold forging depending upon the requirements and there are several different types of forging processes, each with its own set of advantages and disadvantages. The most common types of forging include:
- Hammer forging: In this process, a hammer is used to strike the metal repeatedly to shape it. The metal is placed between two dies, and the hammer is used to apply pressure and shape the metal. Hammer forging is often used to produce large, heavy parts with a high level of strength and durability.
- Press forging: In this process, the metal is placed between two dies and subjected to high pressure to shape it. Press forging can produce parts with a high level of accuracy and a smooth surface finish. It is often used to produce smaller, more complex parts.
- Roll forging: In this process, the metal is passed through a set of rollers that shape it into the desired shape. Roll forging is often used to produce long, slender parts with a high level of strength and a smooth surface finish.
- Upset forging: In this process, the metal is subjected to high pressure to increase its cross-sectional area. Upset forging is often used to produce parts with a high level of strength and durability, such as bolts and rods.
Forging is a popular manufacturing process because it produces parts with a high level of strength and durability. It is also a cost-effective process because it requires little or no material waste. However, it is a labor-intensive process and requires specialized equipment, which can be costly to maintain and operate.
Applications
Forging is a widely used manufacturing process. A few applications of the forging process are given below:
- Gear Manufacturing
- Manufacturing of crankshafts
- Manufacturing of connecting rods
- Aircraft Structural Components
- Turbine Parts Manufacturing
- Axle beams and Shafts
Machining Processes
Machining processes are one of the oldest manufacturing processes. Machining is a process in which material is removed from a workpiece to get the desired geometry. A workpiece can be rotational or non-rotational. Cylindrical workpieces are termed rotational and plate or block-line structural are termed as non-rotational workpieces.
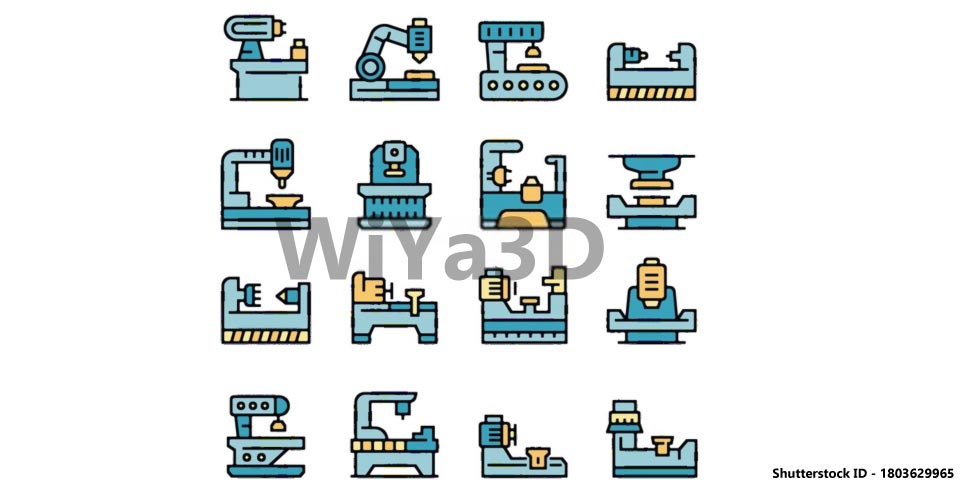
Various Machining Operations are:
- Milling
- Turning
- Facing
- Grinding
- Taper Turing
- Threading
- Boring and Drilling
- Knurling
Machine tools used in various Machining Operations are:
- Lathe Machines
- Milling Machines
- Drilling Presses
- Boring Machines
- Shapers and Planers
Applications
Applications of machining operations include:
- Internal and external Thread Cutting
- Gear Manufacturing
- Rods
- Creating holes of all types
- Furniture
- Nuts and Bolts
Rolling Process
Rolling is a metal forming process in which metal stock is passed through a pair of rolls to reduce its thickness or to make the thickness uniform. The weight of the metal is reduced as it is compressed by the rolls, and the resulting material is often stronger and more durable than the original.
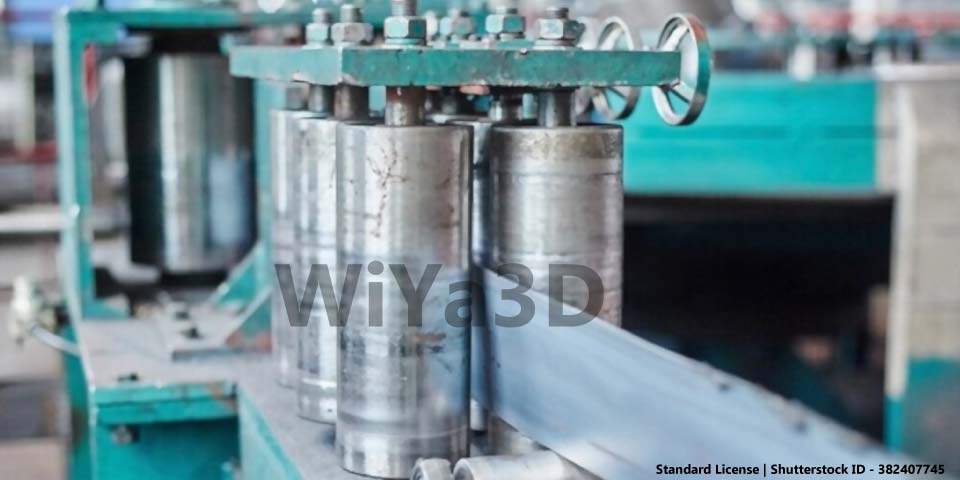
There are several types of rolling processes, including:
- Flat rolling: This is the most common type of rolling process, in which the metal is passed through a pair of rolls to reduce its thickness or to make the thickness uniform. This process is used to produce sheets, plates, and strips.
- Shape rolling: This process is used to produce bars, rods, and other structural shapes. The metal is passed through a pair of rolls with grooves or contours that give the desired shape to the finished product.
- Pipe and tube rolling: This process is used to produce pipes and tubes of various sizes and shapes. The metal is passed through a series of rolls that give it the desired shape and size.
- Ring rolling: This process is used to produce rings and other circular shapes. The metal is passed through a set of rolls that gradually reduce its thickness and increase its diameter to form the finished product.
Applications
Applications of rolling processes include:
- Bars and Rods
- Rails
- Plates, Sheets and Coils
- I-Beams and L-Beams
- U-Channels
- Production of Gears
- Production of Threaded Screws
Extrusion Process
Metal extrusion is a manufacturing process in which a metal billet, or cylindrical log of metal, is placed in a container called a die and forced through a shaped opening to create a long, continuous shape. The process can be used to create a wide range of shapes and sizes, including rods, tubes, and other complex cross-sectional profiles.
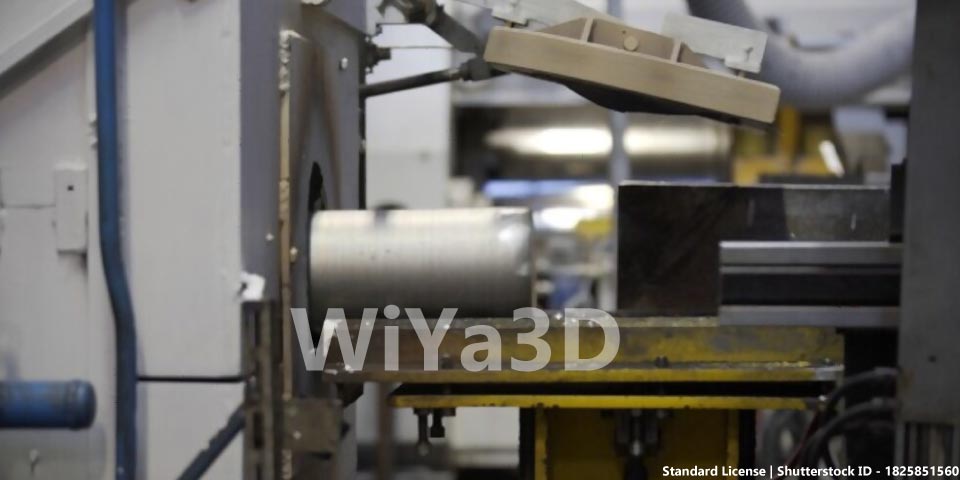
There are two basic extrusion types:
- Direct or Forward Extrusion Process
- In-direct or Backward Extrusion Process
In direct extrusion, the billet is pushed through the die using a ram, while in indirect extrusion, the billet is pushed through the die using a hydraulic ram or a screw. Hydrostatic extrusion uses a high-pressure fluid, such as oil, to push the billet through the die.
The metal extrusion process can be carried out at room temperature or at elevated temperatures, depending on the type of metal and the desired final shape. To achieve the desired shape, the billet may be heated to a plastic state before it is extruded. The extruded metal is then cooled and cut to the desired length.
The metal extrusion process is used to create a wide range of products, including automotive parts, construction materials, and consumer products. It is a cost-effective method for producing large quantities of uniform parts and is capable of producing parts with high precision and close tolerances.
Applications
Applications of Extrusion Process are:
- Manufacturing of hollow tube and long pipes
- Automobile Frames
- Manufacturing of aluminum and steel rods
- Manufacturing of windows and doors of vehicles
- Manufacturing of heat sinks
Wire and Bar Drawing Process
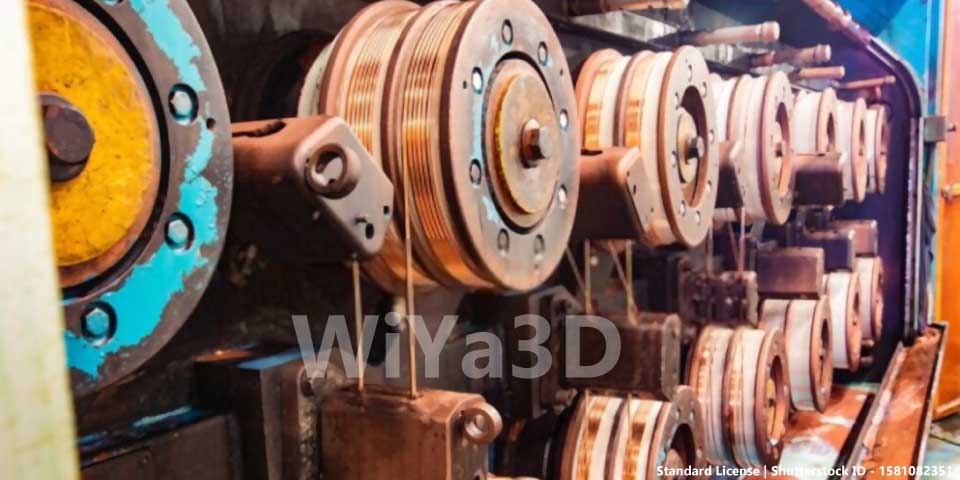
Drawing Process is defined as a process in which a wire or bar is forced (pulled) from a die opening to reduce its cross-section.
It is similar to the extrusion process, however; the workpiece is pushed through a die opening in the extrusion process but in the drawing process work is pulled from the die opening.
In Bar Drawing, the diameter of stock is relatively larger. In Bar Diagram, work is passed through a single die opening and it is known as a ‘Single Draft Operation’. While in wire drawing, the diameter of the workpiece is less than 0.001 in or 0.03 mm. In wire drawing, a long wire is passed from a series of dies to reduce its diameter.
A typical draw die consists of an entry region, approach, bearing surface, and die-relief angle. The entry region is usually lubricated. The approach is the region where the drawing process takes place and the bearing surface determines the final size of the workpiece. Back-Relief is the exit zone where an angle of 30 degrees is provided.
Applications
The applications of wire and drawing process are:
- Wires for fences
- Electric Wires
- Hangers and Shopping Carts
- Screws and Rivets
- Metal Bars
- Springs
Sheet Metal Working
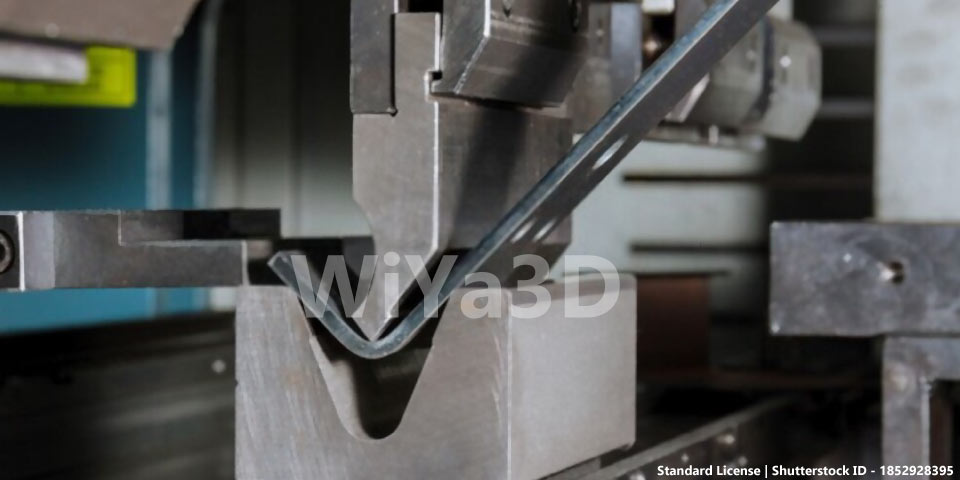
Sheet Metal Working is defined as a process in which Cutting, shearing, and forming operations are carried out on the sheets that are usually 0.4mm to 6.0 mm thick.
Sheet metal working is not performed at high temperatures. These operations are usually carried out at room temperature. Stamping presses are used to perform sheet metal operations on metal sheets. Punch and dies are the tools that are used in sheet metalworking.
Cutting operations performed in sheet metal working includes:
- Shearing
- Punching and Blanking
- Cutting and Parting
- Notching
- Shaving, Trimming and Blanking
- Bending Operation
Bending operations performed during sheet metal working includes:
- V-Bending
- Edge-Bending
Other operations performed on sheets includes:
- Drawing of Metal Sheets
- Ironing
- Coining and Embossing
- Lancing and Twisting
Applications
There are a lot of applications of Sheet Metal working in industry worldwide. A few of them are listed below:
- Body of Automobiles
- Body of Airplanes and other parts
- Locomotives and Railway cars
- Computers
- Office furniture
- Electronics Appliances
- Aluminum Beverage Cans
Powder Metallurgical Process
Powder Metallurgy is a manufacturing Process defined as a process in which metallic powders are pressed and heated to get the desired shape.
Powder metallurgy is the net shape or near-net shape operation. In this process, a punch and die tooling is used to press the metallic powders which are then heated to bond together into the desired shape. The heating of powders takes place below their melting point and it is known as sintering.
Metals are first converted to powders through many methods like:
- Atomization
- Chemical Reduction
- Electrolysis
Metallic Powders are usually expensive and they are difficult to store.
Applications
Powder metallurgy is used in manufacturing of various products that are difficult to manufacture by other manufacturing processes. A few of them are given below:
- Gears and Bearings
- Fasteners
- Cutting Tools
- Electric Contacts
- Parts of various machines
- Tungsten filament of incandescent bulb
Joining & Assembly Processes
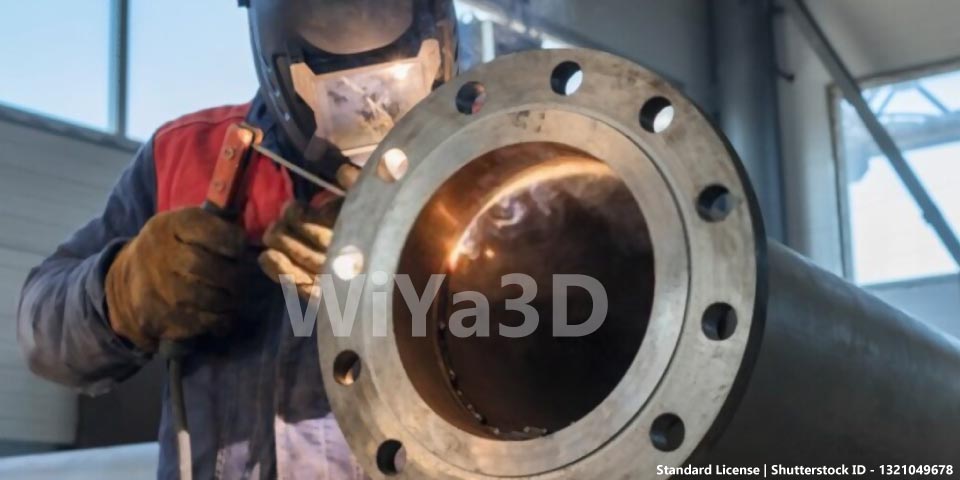
Assembly Process is used to join two or more parts to create a new entity. It is of two main types:
- Permanent Joining
- Mechanical Fastening
Permanent joining is used to create a permanent joint between two or more parts. In Permanent joining, two parts could not be disassembled after they are joined together. Examples of permanent joining includes:
- Welding
- Brazing and Soldiering
- Adhesive Bonding
Mechanical Fastening is used to create a join that can be disassembled easily and quickly if needed. Examples of mechanical Fasteners are:
- Nuts and Bolts
- Rivets
- Press fitting
- Expansion Fitting
Applications
Applications of Assembly operations includes:
- Joining electric Wires through Soldiering
- Threaded fasteners in doors and windows
- Electric and Electronic Appliances
- Beds and Furniture
- Cars and Automobiles
- Aircraft Assembling
- Spaceships and Satellites
Additive Manufacturing
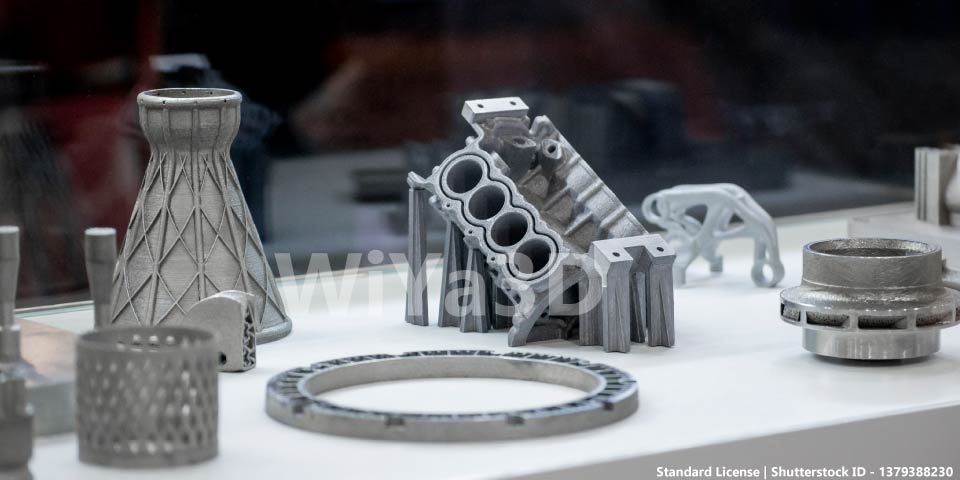
Additive manufacturing, also known as 3D printing, is a manufacturing process that involves building up layers of material to create a three-dimensional object. The process starts with a digital 3D model of the object, which is then used to create a physical object by adding layer upon layer of material.
There are several different technologies that are used in additive manufacturing, including:
- Fused deposition modeling (FDM): This process involves melting a plastic filament and extruding it through a nozzle to create layers of material.
- Stereolithography (SLA): This process involves curing a resin with a laser to create layers of material.
- Selective laser sintering (SLS): This process involves using a laser to fuse together particles of powdered material to create layers of material.
- Electron beam melting (EBM): This process involves using an electron beam to melt layers of powdered metal to create a solid object.
Additive manufacturing has several advantages over traditional manufacturing methods, including the ability to create complex shapes and geometries, a lower cost for prototyping and small-batch production, and a reduced need for tooling. It is used in a wide range of industries, including aerospace, automotive, medical, and consumer products.
Applications
Additive manufacturing is a modern manufacturing technique. A few applications of additive manufacturing are:
- 3D Bio-printing
- Manufacturing of Prosthesis
- Light Weight Satellites
- Manufacturing of light weight tools
- Robotics
- Manufacturing of Complex Geometries that are not possible with conventional manufacturing Methods